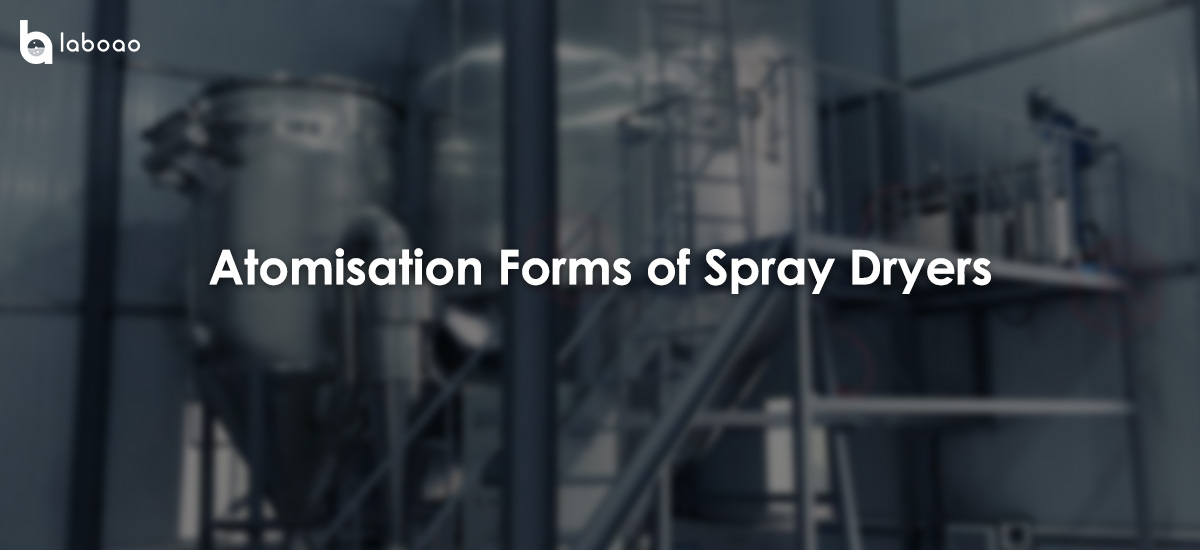
There are three conventional forms of atomisation for spray dryers.
1. rotary atomization, which is characterized by: large production capacity of single machine (the maximum spray volume can reach 200t/h), easy control of feed volume, large operational flexibility, and relatively wide application.
2. Airflow atomisation, airflow atomisation spray dryers are mainly used in laboratories and intermediate plant manufacturers. The material liquid that cannot be atomised by the first two atomisers can be atomised by using the airflow type atomiser. High viscosity pastes, pastes and filter cake materials can be atomised using a three-fluid nozzle. The disadvantage is that the power consumption is large.
3. Pressure-type atomisation, which is characterised by: can create coarse particles, easy maintenance. As the nozzle hole is small, easy to block, so the liquid must be strictly filtered. Nozzle hole is easy to wear, must be made of wear-resistant materials. Pressure nozzle there is a new structure, called pressure - airflow nozzle. It is characterised by a pressure-type nozzle in the centre and an airflow-type nozzle in the surrounding environmental gap. The atomisation is in two stages: the pressure nozzle first forms a liquid film, which is atomised by the airflow for a second time, making the droplets finer.
Spray dryer atomisation advantages.
1. Due to the large surface area of the atomised droplet population, the drying time required for the material is very short (in seconds).
2. In the high temperature air stream, the temperature of the material wetted on the surface does not exceed the wet bulb temperature of the drying medium, and the final product temperature is not high due to rapid drying. Therefore, the spray thousand drying is especially suitable for heat-sensitive materials.
3. High production efficiency, few operators. Large production capacity and high product quality. The spraying volume can reach several hundred tons per hour, which is one of the larger dryer handling capacity.
4. Depending on the flexibility of the spray drying operation, various product quality indicators can be met, such as particle size distribution, product shape, product properties (dust free, fluidity, wettability, quick solubility), product colour, flavour, taste, biological activity and the wet content of the final product.
5. Simplify the process. The solution can be made directly into a powder product in the drying tower. In addition, spray drying is easy to achieve mechanization and automation, reduce dust flying and improve the labour environment.
Spray dryer atomisation disadvantages:
1. When the air temperature is below 150C, the volume heat transfer coefficient is low [23~116W/(m3. K)], and the volume of equipment used is large;
2. High requirements for the separation of gas-solid mixtures, generally requiring two stages of dust removal;
3. Thermal efficiency is not high, generally 30% to 50% for the down-flow tower type, 50% to 75% for the counter-flow tower type.
4. The equipment is more complex, covers an area of large, a large investment.
5. Atomiser, powder recovery device is more expensive.
6. Need more air, increase the power consumption of the blower and the capacity of the recovery device.